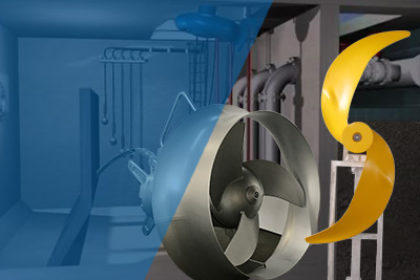
ZQB series submersible axial-flow pump and HQB series submersible mixed flow pump are widely used in Agriculture, Industry and Civil engineering for drainage and water-supply, etc.. These pumps are features for low cost, easy installation, high reliability and can be automatically controlled.
Operation conditions:
1. Maximum medium temperature 50℃
2. PH 5~9
3. For pumping clear water or liquid physical character similar to water or liquid with little solids.
4. The pump can be stared 6-times each hour at the most with equal interval time.
5. Maximum submerged depth is 10 meters.
DESCRIPTION OF CONSTRUCTION
The main feature of pumps are that two kids of seals are used that are effective and reliable moving & static seals. Static seals is suitable foe use in all mating faces of static parts. The mating faces of static parts is equipped with “O” oil-proof rubber sealing ring. The auxiliary sealing material is non-dried sealing glue. Cable is separately, water pressure-tight encapsulated connection with strain relief, anti-kink protection and single lead sealing. Three mechanical seals are used in series between shaft and casing. Two of them are placed in oil chamber, one is used for protecting the motor from liquid leakage, the other for protecting the oil chamber from water. The oil chamber acts as buffer for leakage between the motor and pump, meanwhile mechanical seals and roller bearing are lubricated in it.
The pump insulation is class “F”=155℃
Rotor is aluminum cased squirrel-cage and shaft is stainless steel and has been dynamically balanced
.
At the top of the pump, there is a screw hole which is used for air leakage test before ex-work that each pump has been carried foe a gas leakage test with air pressure 0.15MPa for 5 min..
The rotating part is borne by four bearing. Upper bearing is an centripetal ball bearing, middle bearing is a short cylindrical bearing with a separable internal ring, these bearings with stand radial load. A rubber bearing act as auxiliary role for withstanding radial load. A big size centripetal thrusting roller bearing are used in the pump in order to bear weight of all rotating parts which bearing has low temperature and middle bearings are lubricated by No.3 lithium lubricating grease. All bearing are SKF brand.
Rotating direction of the motors shall be anti-clock wise rotation from the view of shaft according to the requirement of pump.
All pumps are equipped with thermal sensors for monitoring temp. rise of the winding. By lower thrusting bearing, a special sensor is located in oil chamber to monitor temp. rise of thrusting bearing, a device with double electrodes is set at the bottom of inside chamber of motor, if water is leaking into chamber, and reaches a certain high level from the bottom of chamber, the value of the resistance will be varied which will be changed into a switching signal by a water lever relay built in a control device. A electrode stretched out of the lower cover is used to check leakage in oil chamber of pump, and signal is transmitted by a water-level relay in the control device.
The pump has two main power cables and one control cable. Two main cable should be connected in parallel according to the same mark.(U,V,W,) Some pump (power below 90kW without any special requirements) only has one main power cable. See sketch of connection of power cable.
Pump impeller is semi-adjustable. Impeller blades can be adjusted according to the requirement of work by means of unscrewing nuts on the blades, pulling up fixing pin, moving the blades and adjusted the basic line of blade to a required angle line on the hub, then inserting the fixing pin fastening the nuts. Because inner surface of shell of impeller is cylinder, diameter of impeller must be machined after angle of blade is changed (small than that specified in contract). All vanes of delivered pump have been adjusted to the required angle specified in a contract. Users can adjust the vane by themselves, but it shall be paid a green attention to whether over power or over current.
Oil chamber is filled with No.20 machine oil. The volume of stored oil is determined by seeing oil overflowed through hole. For oil chamber, there are two hole separately located by two sides, one is injecting oil, the other is air vent hole. When injecting oil into the chamber, two holes shall be opened. After injecting oil, two holes shall be screwed up with two spigots. It shall be paid great attention to check whether the square seals have been broken.
A rubber bearing is equipped just up the hub of the impeller and is lubricated by water. It offers the impeller more stability and acts as a role of auxiliary bearing.
PREPARATION FOR OPERATING
The structure must be handed over ready for installation and must be dry and clean. In particular the inlet chamber must be empty and dry.
“As built” drawings of the civil work must be available by the client/consulting engineers in good time before starting installation.
Before installation, checking the record of main parts dimensions according to drawing to ensure that they can be connected smoothly. Inspecting and cleaning flange connecting surfaces.
For no load running on the ground, running time must be less than 15 seconds.
Checking the insulation resistance of the stator’s winding with a ohm meter of 500MΩ class, and never allow lower than 0.5 MΩ. The protective devices also need to be checked with a universal meter in 1K Ω position according to the requirement.
A trash screen shall be put in front of inlet channel.
Checking the frequency and voltage of power, whether it is meeting with the value specified in nameplate, the deviation of frequency is 1%, voltage deviation is±5%.